The MAADI Group engineering firm, Montréal, Québec, has acquired a Dimension1200es Series Fused Deposition Modeling (FDM) 3D printer.
January 7, 2013—MONTREAL, CANADA – The printer enables MAADI engineers to validate new aluminum extrusions for their many 3D CAD-designed innovative projects.The printer’s FDM 3D models allow testing and improvement of part functionality using the production-grade thermoplastic, ABS plus.
MAADI Group engineers used the new Dimension 3D Printer with ABS plus material to create a working 3D model of the specially-designed red-colored latching system for recently installed service bridges, using FDM to form 3D latches that securely lock the aluminum barriers closed. The twin 20-meter-long aluminum pedestrian service bridges are utilized at Rio Tinto Alcan’s smelting furnaces in Jonquière, Québec, Canada. The service bridges required a tough latching system because they have side entry openings with removable barriers that enable worker access to the furnaces. The bridge is placed next to the furnace and the worker gains access by removing the security barrier.
ABS plus is an ideal material to facilitate conceptual prototyping, allowing MAADI designers to achieve component design verification through direct digital manufacturing. The FDM technology combined with ABS plus material enables MAADI engineers to create functional parts such as the latch system. MAADI uses digital Computer Aided Design (CAD) software that results in a strong (Fy 5400 psi) working part, with a smooth finish and more feature detail.
In FDM technology, ABS plus materials are heated in an extrusion head and are deposited in a thin-layered model that, when removed from its support materials, becomes an accurate, durable and functioning 3D model that performs like a production part. MAADI Group CEO, Alex de la Chevrotière, P.E., says, “The 3D printer’s main benefit for us is to validate each of our customer and in-house 1/1-scale extrusion designs and their associated features, such as snap-fit, hinges, interconnections between grooves, and general appearance for an architectural review. Once the design is approved, we send our CAD files out for die production.”
“We now work with functioning models to make sure that our innovative project components all fit together precisely, before we go into full production,” continues de la Chevrotière, “There is a huge savings in time and money by making accurate adjustments in the early prototyping stage, which allows us to correct issues before they become problems. Having a 3D model in hand assures that our end product meets every customer requirement and works perfectly, just as the designer envisioned.”
De la Chevrotière, notes:“In addition to MAADI Group’s aluminum service bridges, we will use FDM 3D models for upcoming structural design projects, including a new architectural anodized aluminum screen. This design was made in collaboration with Yelle & Maillé Architects (Montreal, Canada), and consists of interconnecting horizontal and vertical extrusions that form an aesthetically pleasing architectural screen for the front of an older hospital building. The printed extrusion section model (6” x 14” x 12”) confirms the visual appearance of the final product.”
MAADI Group recently printed a 3D aluminum bridge deck section model that was featured in a November press conference in Montreal to publicly demonstrate the advantages of this powerful aluminum extrusion tool for infrastructure design, and specifically, for designing bridge structures. The 3D model required just eight hours and a few hundred dollars to create a precise and realistic model, compared to several months and thousands of dollars that an aluminum product sample typically requires.
“We view the acquisition of our Dimension 3D printer as a tremendous asset to our engineering capabilities, enabling us to add specialized features for our customers,” says de la Chevrotière, “In our furnace service bridges for Rio Tinto Alcan, workers gain added security by releasing the ABS plus latches to open the bridges’ side barriers, secure their safety equipment, accomplish their work, then re-secure the barriers in place with the built-in latching system when exiting the bridge. The convenience of incorporating a built-in latching system as an integral part of the service bridge structure greatly increases efficiency, while maintaining the highest level of safety. If this latching system had been milled using a conventional NC milling machine from plain aluminum bars and backed paint thereafter, the final cost would have been four times more than with our 3D printed latches and would have taken a month, compared to only 12 hours of printing time!”
The FDM 3D ABS plus printed parts have the precision and durability to integrate well with the extruded aluminum components that MAADI Group designs for their many innovative marine, civil and architectural structures. The benefits of 3D prototype modeling, combined with extruded aluminum structural design versatility make MAADI Group’s aluminum projects efficient, cost-effective solutions for today’s applications.
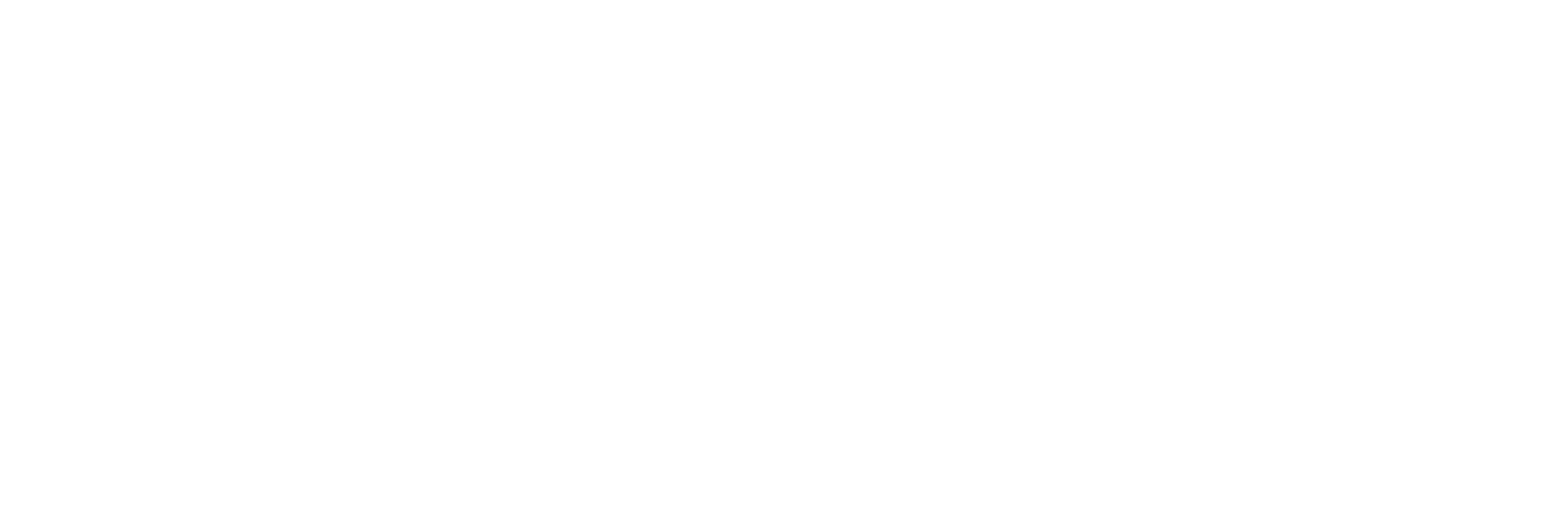